Revolutionizing Mining Operations: Predictive Maintenance Powered by AI
Author: Bhavna Prakash, Solutions Architect – Applied AI Practice
Introduction
The mining industry faces relentless pressure to optimize operations and maximize productivity. Equipment reliability and efficiency are paramount to achieving these goals. Unforeseen equipment failures disrupt production schedules, elevate costs, and compromise safety. Traditional, reactive maintenance approaches, reliant on scheduled inspections or addressing failures after they occur, are no longer sufficient.
Historically, mining has not been synonymous with technological innovation. Today, however, there’s a mounting pressure to innovate and find technological solutions to address challenges ranging from environmental stewardship to operational efficiency and cost optimization.
This article dives into the technical and business aspects of leveraging AI for predictive maintenance in the mining industry. It also critically explores the technical aspects, outcomes, business benefits, and future of AI in mining.
Shifting Gears: From Reactive to Proactive Maintenance
Reactive maintenance, characterized by manual activities like scheduling inspections and recording maintenance data, offers limited control over equipment health. AI, on the other hand, empowers proactive maintenance by analyzing data and predicting equipment failures before they occur. This necessitates a multi-pronged approach:
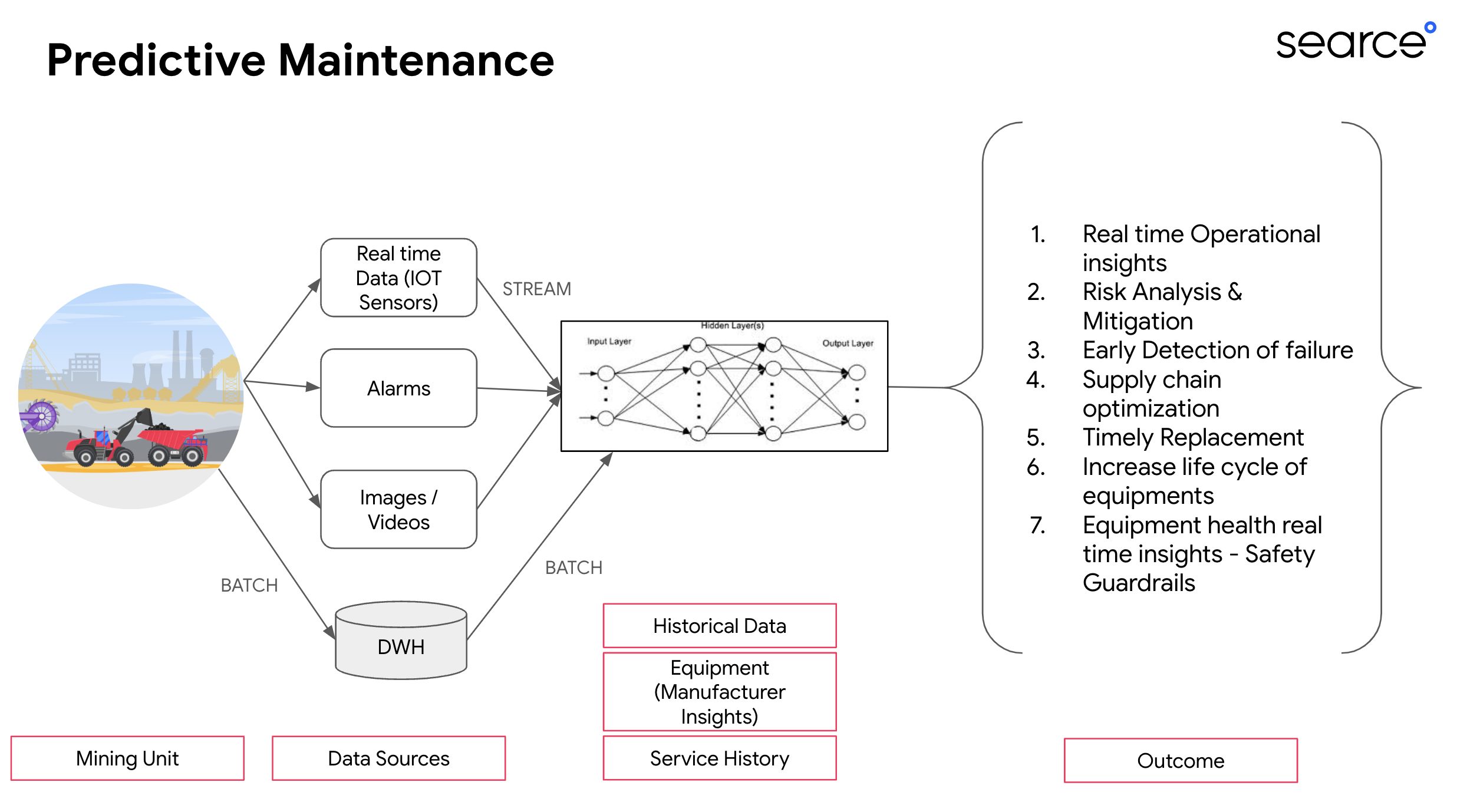
1. Mining Environment and Data Collection
Mining Equipment:
A diverse range of equipment, from excavators to conveyors, forms the backbone of mining operations. Integrating sensors and IoT devices into this machinery delivers real-time insights into equipment health, energy consumption, and environmental conditions.
Data Sources:
- Sensor data & Mining IOT (environment readings from equipment and smart meters)
- Maintenance records (repair, replacement & downtime logs)
- Operational data (production manufacturer insights, environmental factors)
- Alarms
Data Acquisition:
Sensors embedded in the mining equipment collect real-time data on various parameters. Historical maintenance records and operational data like production rates and environmental factors are used for training (or grounding) off-the-shelf AI/ML models specific to the mining operation.
2. Data Processing and Feature Engineering
Data preprocessing removes noise and inconsistencies, preparing it for model training using techniques such as:
- Data Cleaning
- Normalization
- Feature Extraction
3. Machine Learning Models for Predictive Maintenance
Several ML algorithms can be utilized for predictive maintenance, providing different outcomes.
- Predict remaining useful life of equipment
Leverage supervised learning regression models like Linear Regression and Support Vector Regression to analyze historical data to predict time to failure. - Identify Known Anomalies/Health Condition
Utilize classification models (ensemble approach) like Random Forest, Logistic Regression to identify sensor data anomalies indicative of the health of the equipment. - Detect Unusual Patterns/Unknown Failure Reasons
Employ unsupervised learning anomaly detection models like K-Means Clustering to identify unusual patterns in sensor data without pre-existing labels. - Analyze Complex Patterns/Failure Prediction
Implement Deep Learning – Convolutional Neural Networks (CNNs) to analyze sensor data and understand complex patterns signaling potential failures. - Prescriptive Actions /Next Best Steps
Harness Generative AI to recommend the most effective course of action for specific issues based on existing knowledge base, SOP and process documents. - Risk Assessment
Leverage AI/ML to assess and prioritize risks, and understand their impact to operations.
4. Model Monitoring and Retraining
Once deployed, AI models require continuous monitoring using key performance indicators to assess their effectiveness and determine when retraining is necessary. Some metrics to watch out for include:
- Mean time between failures.
- Mean time to repair.
- Equipment Availability.
- Time to repair.
- Time to install.
- Time to procure.
5. Utilizing AI Insights
The AI model’s output can be integrated into existing technology stacks like operational dashboards, chatbots, or mobile apps to provide real-time operational insights. The consumption of the operational insights can happen in the form of a multi conversational app, virtual assistant, operational dashboard on a handheld device.
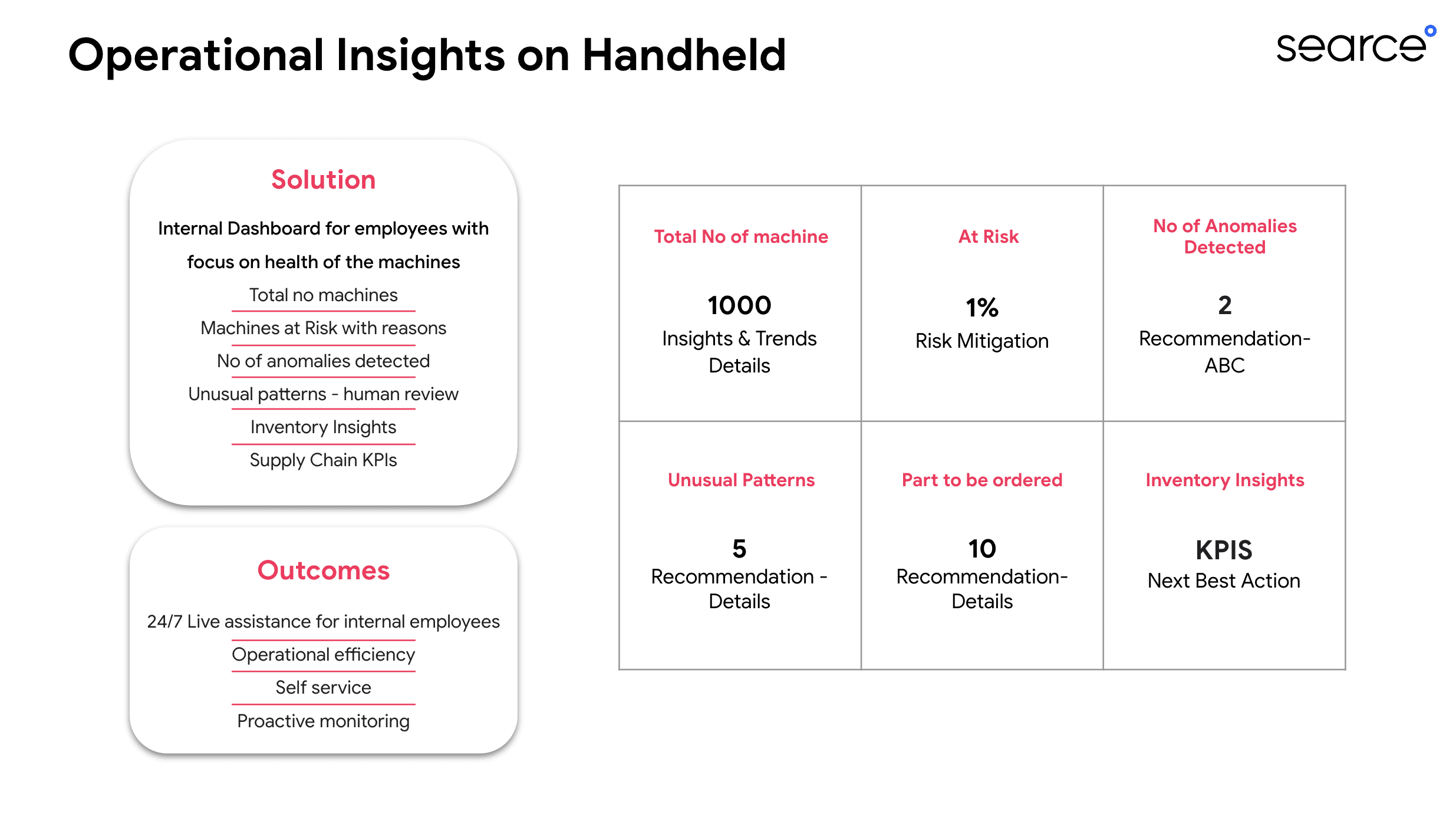
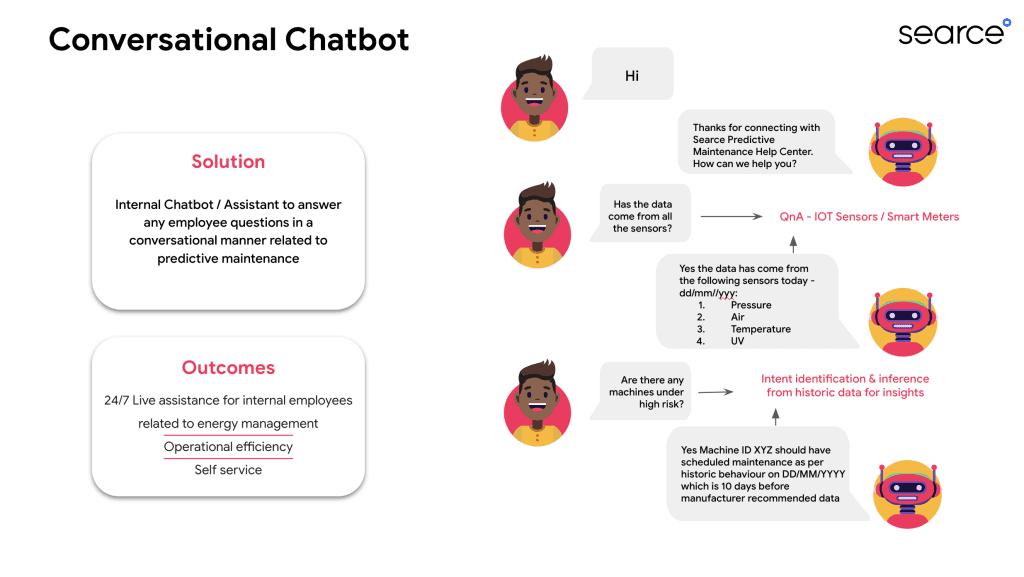
Business Benefits of Predictive Maintenance: Heralding a Paradigm Shift
The mining industry, a cornerstone of many economies, faces unprecedented pressures to boost productivity, reduce costs, and minimize environmental impact. Australia, a mining powerhouse contributing $450 billion annually to GDP (according to Australia Minerals), exemplifies these challenges. Despite employing 1.2 million people, the industry grapples with declining productivity and escalating labor costs.
AI-driven predictive maintenance offers a transformative solution. By shifting from reactive to proactive maintenance, mining operations can significantly enhance efficiency and profitability. As operations scale, the complexity of managing equipment and data grows exponentially, making AI indispensable for gaining actionable insights.
Real-time monitoring of hundreds of machines, each generating millions of data points per second, surpasses human capabilities. AI’s ability to analyze this data deluge provides a comprehensive view, enabling predictive maintenance, anomaly detection, and prescriptive actions. This data-driven approach is essential for optimizing equipment lifespan, reducing downtime, and ensuring operational resilience.
Ultimately, AI empowers mining companies to achieve a new level of operational excellence, driving sustainable growth and a competitive edge.
Implementing a data-driven predictive maintenance approach leveraging AI delivers a multitude of business benefits for mining operations.
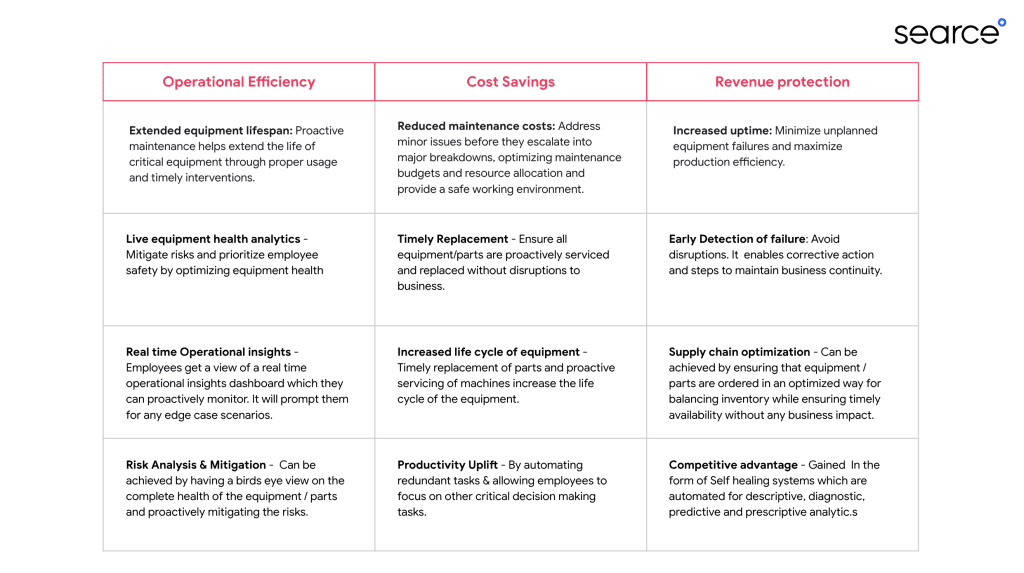
Looking Forward: The Expanding Frontier of AI in Mining
As per a Harvard Study – AI has the power to reduce 610 million tonnes of CO2 emissions, save a 1000 lives, prevent 44000 injuries, and create a value of $320 billion for the mining industry over the next decade. AI’s transformative power in the mining industry extends beyond predictive maintenance. Here’s a glimpse into the future:
- Exploration: Utilize computer vision to analyze geological data, terrain, and satellite imagery for deposit identification and characterization.
- Waste Management: Employ AI-powered image analysis to efficiently segregate waste from valuable ore.
- Environmental Stewardship: Leverage AI and data analytics to minimize environmental impact and optimize resource utilization.
- Effective Transportation: Enhance logistics with AI-driven route optimization, considering real-time factors like traffic, weather, and terrain.
- Real-time Operations: Employ video/image insights, IOT devices, wearables and sensors to create a comprehensive operational dashboard, enabling proactive decision-making.
- Intelligent Customer Interaction: Deliver seamless experiences via interactive conversations, intuitive navigation and relevant answers without a human agent or website search.
- Predictive Analytics: Optimize demand forecasting, pricing, product offerings, and supply chain operations using AI.
- Drilling optimization: Enhance drilling efficiency through data-driven insights and AI-powered recommendations.
The role of AI-powered predictive maintenance in changing the face of the mining industry by reducing downtime, enhancing equipment efficiency, and driving cost savings is unprecedented. As the industry continues to embrace digital transformation, AI’s ability to predict potential failures and optimize maintenance schedules is a game-changer, empowering mining companies to stay competitive in a rapidly evolving market.
Want to learn how AI can enhance your mining operations? Reach out to Bhavna Prakash, our expert in AI-driven business processes, or connect with the specialists at Searce to explore how we can help you transform your mining business with cutting-edge AI solutions.